Trivalent Zinc vs. Hexavalent Zinc Plating for Springs: Choosing the Right Surface Finish Introduction
Introduction
When it comes to enhancing the durability and corrosion resistance of springs, choosing the right surface finish is crucial. Two popular options for spring plating are trivalent zinc and hexavalent zinc plating. This blog explores the characteristics, advantages, and considerations of each method to help businesses make informed decisions for their spring manufacturing processes.

Trivalent Zinc Plating
Trivalent zinc plating is a more environmentally friendly alternative to hexavalent zinc plating. It involves the deposition of a zinc coating onto the spring’s surface through an electrolytic process. Here are some key points to consider when evaluating trivalent zinc plating:
Environmental Friendliness: Trivalent zinc plating produces significantly fewer harmful fumes and waste by-products compared to hexavalent zinc plating. This makes it a more sustainable choice for businesses aiming to reduce their environmental footprint.
Salt Spray Life: Springs plated with trivalent zinc coatings generally exhibit salt spray resistance ranging from 96 to 240 hours. This makes them well-suited for moderate corrosion protection requirements.
Aesthetic Finish: Trivalent zinc plating provides a bright, attractive finish with a consistent appearance. This can be important if the springs will be visible in the final product.
Thickness Control: Businesses can control the thickness of the trivalent zinc coating to meet specific requirements, ensuring that the springs maintain their desired dimensions.
Hexavalent Zinc Plating
Hexavalent zinc plating is a more traditional method that involves the use of hexavalent chromium compounds in the plating process. Here are some key considerations when evaluating hexavalent zinc plating:
Durability: Hexavalent zinc plating offers robust corrosion resistance, making it suitable for springs subjected to extreme conditions, including high temperatures and aggressive chemicals.
Salt Spray Life: Springs subjected to hexavalent zinc plating exhibit excellent salt spray resistance, typically ranging from 240 to 500 hours or more. This level of corrosion protection is suitable for applications exposed to severe environmental conditions, such as extreme temperatures and aggressive chemicals.
Cost Efficiency: Hexavalent zinc plating is often more cost-effective in terms of materials and processing costs, making it a practical choice for budget-conscious businesses.
Process Complexity: The plating process for hexavalent zinc can be more complex and requires careful monitoring and control to achieve consistent results. This may require more extensive equipment and expertise.
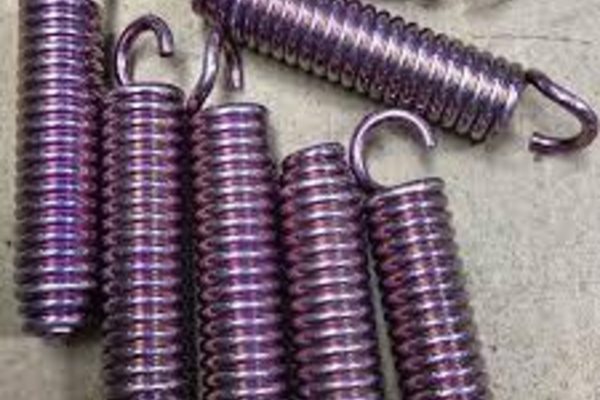
Choosing the Right Plating Method
The choice between trivalent zinc and hexavalent zinc plating for springs ultimately depends on your specific needs, priorities, and constraints. Consider the following factors when making your decision:
Environmental Regulations: If your business operates in an area with strict environmental regulations or is committed to sustainable practices, trivalent zinc plating may be the preferred choice.
Application: Assess the conditions in which your springs will operate. Consider factors like temperature, humidity, and exposure to corrosive substances when selecting the plating method.
Cost effectiveness: Evaluate your budget constraints and cost considerations. Hexavalent zinc plating may be more cost-effective for some applications, but be mindful of its environmental implications.
Aesthetic Requirements: If the appearance of the springs is a key consideration, trivalent zinc plating may offer a more visually appealing finish.
Expertise: Assess your surface treatment vendor’s expertise and equipment capabilities. Hexavalent zinc plating may require a higher level of technical know-how.
Conclusion
The choice between trivalent zinc and hexavalent zinc plating for springs is a critical decision for businesses in the spring manufacturing industry. Consider your environmental goals, application requirements, budget, and expertise when making your decision. In doing so, you’ll be able to select the plating method that best meets your specific needs while maintaining the highest standards of quality and performance for your springs.